INSPECTION SERVICES
We provide inspection services on all lifting, rigging, height safety & confined space equipment to ensure your equipment is safe for use & complies with the relevant Australian Standards.
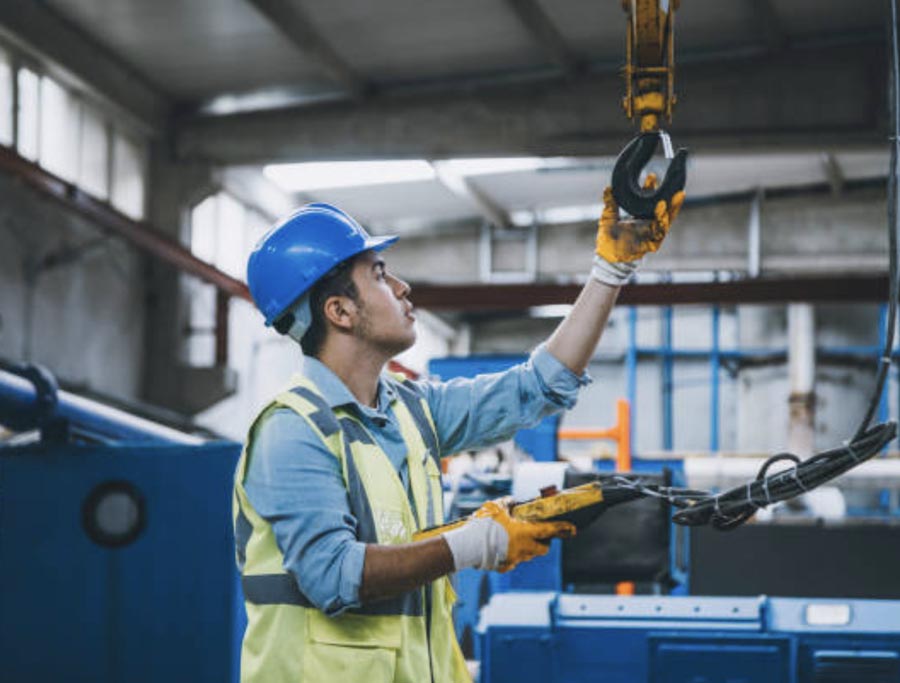
Inspections
Regular inspections & maintenance of lifting gear is required to ensure your equipment is safe for use. All inspections are undertaken by our highly skilled & knowledgeable personnel and can be completed onsite or at our workshop.
An electronic lifting register is compiled and made available instantly following the inspection, which is accessible via our website through your client login. Our clients find this convenient, particularly if your lifting equipment is sent to various sites and you need immediate access to the register.
We work with your team to create an inspection schedule that suits your requirements & complies with Australian Standards.
REPAIRS
When your equipment doesn’t pass an inspection, we will advise the safest and most cost-effective option for your business, whether that is to repair or replace the equipment.
In the instance where your equipment needs repair, we ensure the turn around time provides minimal disruption to your business.
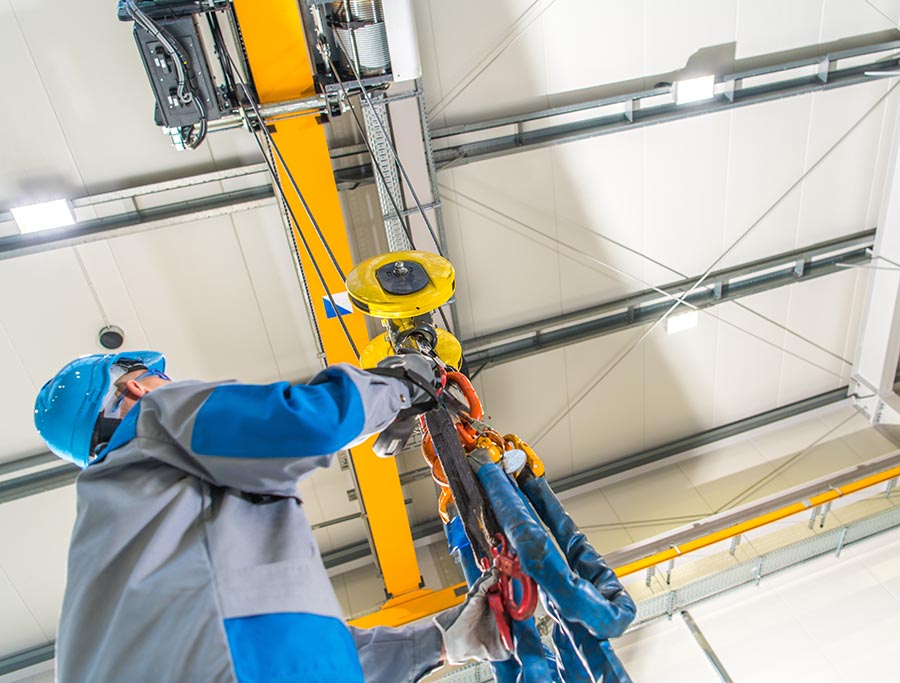

Height Safety
We can provide inspection and certification of your height safety & confined space equipment. If you require repairs, replacement, or custom application, we can arrange this with our heights safety suppliers & manufacturers.
Here is a general list of the height safety items we inspect:
- Heights Safety Harnesses
- Attachment Straps
- Lanyards
- Temporary Safety Lines
- Rescue Equipment
- Confined Space Harnesses
- Attachment points
- Horizontal Static Lines
- Inertia Reels
- Fall Arrestors
INSPECTION TAGS & BOARDS
Tags are placed on your equipment during an inspection and the colour represents which quarter of the year the test was performed. Our inspection tags can be customised to ensure visibility & traceability of your assets.
We can supply inspection boards to be placed in a central area of your business, for example, the pre start/muster area, rigging storage area or the safety notice board. The inspection boards have your company logo as well as the current colour for the quarter, and our contact details.
On request we can also supply an out of service cage, complete with signage and out of service tags or stickers. This ensures all staff know that the equipment placed in the cage is not serviceable and not to be used. This also creates a central place for us to check, depending on your requirements, quarterly, monthly or even weekly in some cases.
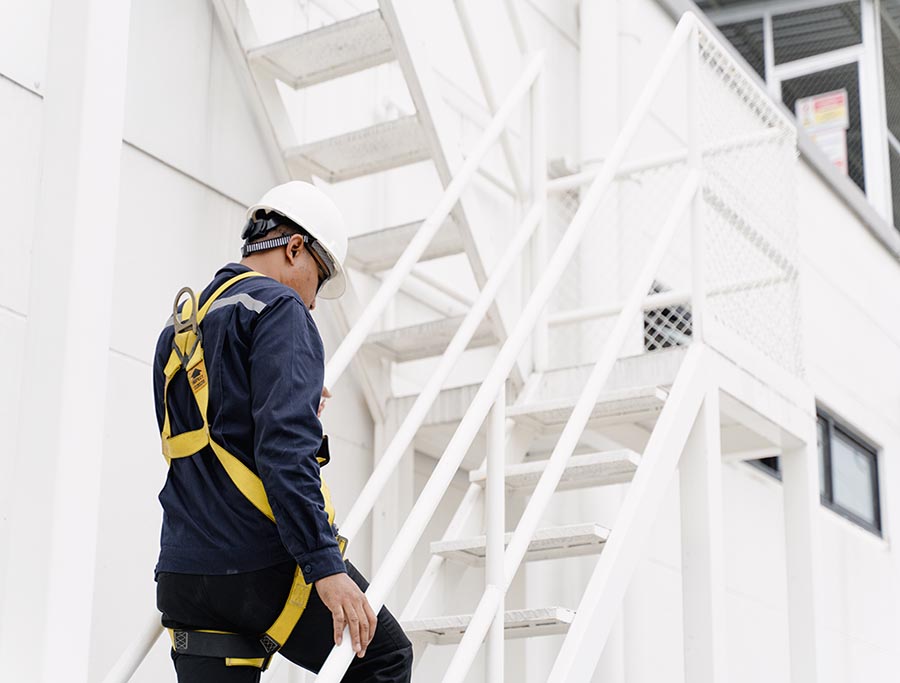
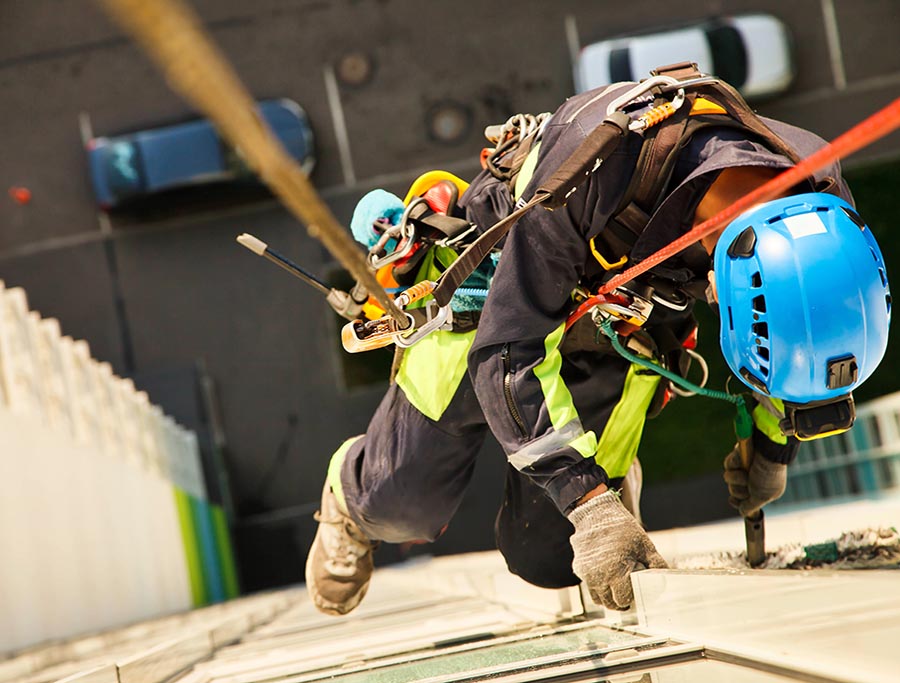
Online Asset Management System
We have partnered with Core Inspection Software to provide a reliable and convenient asset management system to keep track of your lifting equipment & maintain your compliance requirements.
When we conduct an inspection of your lifting equipment, the results are made available immediately through the online register portal on our website.
From the portal, you can view your equipment register, download certificates and keep track of your equipment. This has proven to be convenient and reliable, particularly if your equipment moves across multiple sites.